Waldrich Coburg MultiTec 2000 AT CNC Double Column Planer-Type Milling Machine with 7 Controlled Axes and 2 Tables
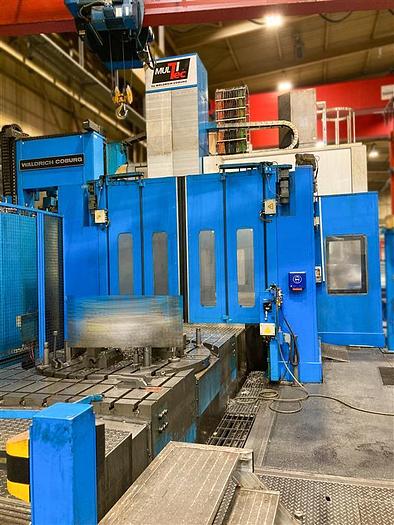
Waldrich Coburg MultiTec 2000 AT CNC Double Column Planer-Type Milling Machine with 7 Controlled Axes and 2 Tables
Description
SPECIAL FEATURES:
Equipped with a double table, the portal machining center can be used in efficient pendulum operation or coupled for particularly large workpieces up to 6,000 mm in length and a maximum weight of 30 tons. The machine features a rotary table with a diameter of 1,750 mm on the front table for vertical turning operations. The high rigidity of the portal design ensures outstanding machining quality and precision in the production of workpieces. Thanks to the automatic exchange system for 160 tools and 4 machining units, as well as a rotary table for vertical turning tasks,
the machine impresses with exceptional versatility, precision, and efficiency, even in multiple productions. Combining precision, flexibility and performance, this portal machining center is ideal for demanding manufacturing tasks in various industrial sectors.
FEATURING:
- Siemens SINUMERIK 840D CNC Control
- Automatic Tool Change System for 160 Tools and 4 Processing Units/Heads
- VERTICAL SPINDLE UNIT: Type VS 125 C/400
- Max. power 45 kW
- Rated speed 330 rpm
- Max. torque 1,250 Nm
- Max. rotational speed 6,000 rpm
- Tool holder ISO 50
- HORIZONTAL SPINDLE UNIT: Type HS 125 C
- Max. power 45 kW
- Rated speed 330 rpm
- Max. torque 1,250 Nm
- Max. rotational speed 6,000 rpm
- Tool holder ISO 50
- Tool clamping force 25 ± 2,5 kN
- NC-UNIVERSAL SPINDLE UNIT: Type GSC 125 C
- Max. power 45 kW
- Rated speed 350 rpm
- Max. torque 1,250 Nm
- Max. rotational speed 6,000 rpm
- Tool holder ISO 50
- Tool clamping force 25 ± 2,5 kN
- Automatic swiveling in the vertical plane (NC) ± 95°
- Swiveling speed (B-axis) 3,600°/min
- TOOL CARRIER for modular tools: Type VHST 500 C
- Tool holder ISO 50
- Tool clamping force 25 ± 2,5 kN
- Automatic tool clamping
- Internal and external coolant supply
- Emulsion mist and dust extraction system
- Electrostatic air filter for oil/emulsion mist separation with electronic dirt indicator
- Cartridge filter for the separation of dusts with automatic compressed air cleaning and dirt indicator
- Control for both systems
- Noise protection measures
- Collection container
- Adaptive control (dependence of spindle power on feed rate)
- Cleaning station for tool taper
- Measurement probe MP3
- Measurement data logging including printer
- Drill Break Detection
- Tool life monitoring
- ARTIS - tool monitoring
- Chip conveyor system: right & left over the entire bed length
- Additional flushing nozzles in the chip conveyor area
- Additional cross conveyor at the end of the bed
ROTARY TABLE FOR VERTICAL TURNING
- Faceplate diameter 1,750 mm
- Swing diameter 2,000 mm
- T-Slots in longitudinal direction 28 H8 U/min
- Distance 250 mm
- Max. Drive power (100% duty cycle) 63 kW
- Speed continuously variable up to 300 rpm
- Rated speed 30 rpm
- Max. Torque in turning operation 18,800 Nm
- Speed range in C-axis operation 0 - 7.5 rpm
- Max. Torque in C-axis operation 9,400 Nm
- Max. Holding torque in clamped position 40,000 Nm
- Positioning accuracy ± 3 sec
- Rotary table load capacity 12,000 kg
TABLE DIMENSIONS (Double Table Configuration)
- Clamping Width of Both Tables 1,750 mm
- Clamping Length of Front Table 3,000 mm
- Clamping Length of Rear Table 2,000 mm
- Clamping Length with Coupled Tables 6,000 mm
- T-slots in longitudinal direction H8 28 mm
- Distance 250 mm
- Max. table load front table 20,000 kg
- Max. table load rear table 20,000 kg
- Max. table load with coupled tables 30,000 kg
- per table 15.000 kg
FEED RATES
Table, longitudinal 0 - 60,000 mm/min
Table, longitudinal (X-axis) 0 - 60,000 mm/min
Milling and drilling unit horizontal (Y-axis) 0 - 60,000 mm/min
Spindle slide, vertical (Z-axis) 0 - 60,000 mm/min
Crossbeam, vertical (W-axis) 0 - 6,000 mm/min
COOLANT - Feed performance at the milling and drilling unit
- for external coolant supply 80 l/min - 1 bar
- for internal coolant supply 40 l/min - 10 bar
15 l/min - 27 bar
CHIP REMOVAL SYSTEM
- Hinged belt conveyor, usable width: 225 mm
- Longitudinal conveyor: right & left over the entire bed length with discharge onto cross conveyors
- Cross conveyor: at the end of the machine bed with discharge into a container
CONTROL SYSTEM:
The SIEMENS SINUMERIK 840D CNC control is equipped with a 19" machine control panel, a flat operator panel
OP031 with a 10.4" TFT color flat screen, and a handheld operating device Type B-MPI.
Included software options:
- Technological cycles
- Quadrant error compensation via operation
- Profibus
- Safety Integrated safety functions for personnel and machine protection
- Remote diagnostics "HOST" for MMC 103
- NC extension:
- Adaptive Control (Automatic feed adaptation)
- Included NC options for spindle unit GSC 125 C:
- Look ahead
- 5-axis machining package
- Multi-axis interpolation
- 3D tool radius compensation
- Feed interpolation
- SINDNC including Ethernet network connection
CONSTRUCTION:
BED AND TABLE
The bed is made of DuoCom, and the table is made of high-quality gray cast iron. Both are dimensioned to accommodate the workpiece weight and clamping device, as well as high cutting forces without affecting machining accuracy. Surfaces machined with the highest precision on the machine bed serve to mount the hardened and ground guide rails for the longitudinal adjustment of the table.
Steel telescopic covers at both ends of the table protect the bed guides. Modules between the individual cover boxes ensure an even, positively guided transmission of the traverse movement, achieving absolutely shock-free feed and rapid traverse movements. Surfaces are provided on the underside of the bed for placement on leveling wedges. With these leveling wedges, the bed is firmly anchored horizontally and vertically to the foundation.
DUOCOM
DuoCom is a composite construction of steel and steel fiber-reinforced mineral concrete. The steel shell of the frame components is dimensioned to absorb all static and dynamic loads. The steel fiber-reinforced mineral concrete increases static and dynamic rigidity. Additionally, damping and thermal stability are significantly enhanced.
DOUBLE TABLE DESIGN
Each table has its own drive. In double-table operation, one table is parked for loading and unloading. In single-table operation, both tables are coupled and moved synchronously together.
Coupling of the two tables is automatic. Clamping bolts according to DIN 69872 are provided on the coupling side of one table. On the coupling side of the other table are collets into which the clamping bolts enter when the tables are brought together. The tables are firmly clamped together with disc springs. The opening of the collets is hydraulic.
Steel telescopic covers between the individual tables protect the bed guides.
CROSS BEAM
The cross beam is made of DuoCom. The distance between the working spindle and the front edge of the cross beam is minimized, increasing stability during machining. Surfaces machined with the highest precision receive the hardened and ground guide rails for guiding the milling and drilling unit. Aluflex covers on both sides of the milling and drilling unit protect guides, racks, and measuring systems.
AUTOMATIC POSITION COMPENSATION OF THE CROSS BEAM
The parallel alignment of the cross beam to the machine table is achieved via a linear measuring system on each column. The drive system maintains each side in the predetermined W-axis position via the CNC, ensuring exact parallel alignment of the cross beam for every machining situation (cross beam and support adjustment).
MILLING AND DRILLING UNIT M4:
MAIN DRIVE AND MILLING GEARBOX
The drive motor and milling gearbox are integrated as a unit within the spindle carriage in a protected manner.
The liquid-cooled AC servo motor is dynamically balanced, reversible, and finely controllable. It drives the drive shaft to the spindle units via the milling gearbox.
The milling gearbox is designed as a 2-speed unit, featuring helical, case-hardened, and ground spur gears of high quality.
Shifting of the gearbox stages is pneumatic. The end positions are monitored by limit switches and mechanically held by a detent, ensuring that the shift position is securely maintained in the preselected stage in case of power failure.
- Drive power (100% duty cycle) 45 kW
- Speed range 1st gear: 5 - 1,300 rpm
- Speed range 2nd gear: 23 - 6,000 rpm
- Rated speed 330 rpm
- Max. torque (100% duty cycle) 1250 Nm
- Cross-section of the spindle slide 400 x 400 mm
LUBRICATION AND COOLING
Lubrication of the gear meshes and bearing points in the milling gearbox is carried out via a lubrication circuit. The lubricating oil is cooled, filtered, and ensures minimal efficiency losses due to its special properties. Housing and motor cooling are managed through a separate cooling circuit.
These measures guarantee constant geometrical accuracies regardless of the spindle speed.
TABLE DRIVE
The table drive operates via a pinion/rack system. The gearbox is mounted on the table. Two mechanically preloaded pinions engage backlash-free into the helical rack in the machine bed.
DRIVE OF THE MILLING AND DRILLING UNIT ON THE CROSS BEAM
The drive operates via a pinion/rack system. The gearbox is mounted on the lower slide. Two mechanically preloaded pinions engage backlash-free into the helical rack on the cross beam.
DRIVE OF THE CROSS BEAM
Adjustment of the cross beam is carried out via ball screw spindles. Each spindle is driven by its own feed gearbox with a feed motor. The two drives are synchronized via the CNC.
COLLISION AND APPROACH SAFETY DEVICES
Lag error monitoring devices in the NC and current limiting devices for the drives switch off the drive motors of the machine axes in the event of a collision or overload.
SINUMERIK Safety Integrated provides effective personnel and machine protection in accordance with the EU Machinery Directive and meets the requirements of Safety Category 3 according to EN 954-1.
GUIDE SYSTEMS
The guides of the X, Y, Z, and W axes consist of roller recirculating units that run on hardened and ground guide rails. Special guide rails and completely enclosed guide carriages provide the highest rigidity concerning compression, tension, and transverse loads.
The systems are extremely rigid and maintenance-free, enabling high adjustment speeds. Lubrication of the roller recirculating units is automatic with grease. The X, Y, Z, and W axes are held in position by a backlash-free motor brake when the feed motor is switched off. For the vertical axes Z and W, there is a second holding brake available.
Specifications
Manufacturer | Waldrich Coburg |
Model | MultiTec 2000 AT |
Year | 2002 |
Condition | Used |
Stock Number | 11149 |
Spindle speeds | 6,000 rpm |
X axis travel | 7,000 mm |
Y axis travel | 3,000 mm |
Z axis travel | 1,500 mm |
Table size, coupled | 6,000 mm |
Table capacity, coupled | 30 Ton |
Rotary table diameter (VTL style) (x2) | 1,750 mm |
Rotary table capacity (VTL style) (x2) | 12 Ton |
C axis, swivel around Z axis (table of spindle unit) | 360° / 1° |
B-axis: GSC 125 C, swivel around Y-axis and X-axis | 360° / 0.001° |
C1 axis: rotary table faceplate diameter | 360° / 0.001° |
Number of controlled axes | 7 |
W axis travel, vertical crossbar | 1,000 mm |
Z + w axis (ram + crossrail) | 2,500 mm |
Ram cross section | 400 x 400 mm |
Spindle drive motor | 45 kW |
Spindle taper | ISO 50 |